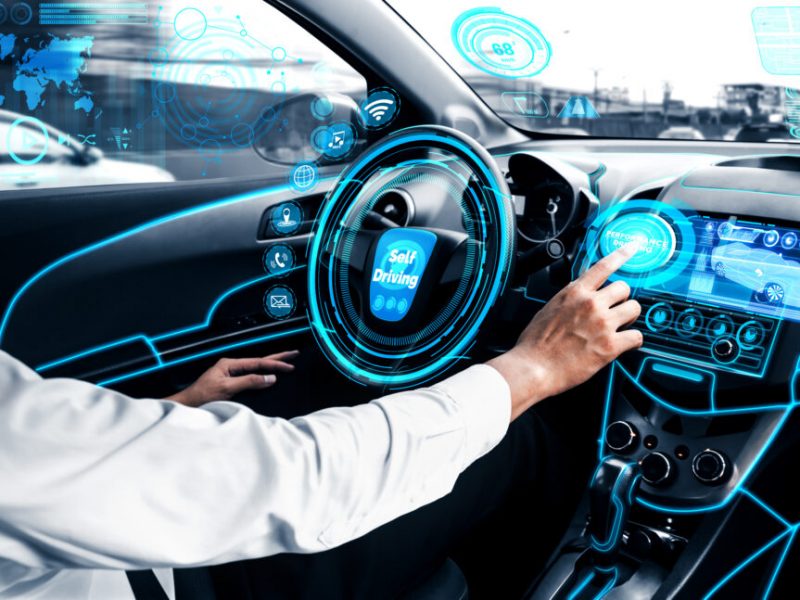
Friday, Feb 26, 2021, 4:30pm
by Falan Yinug, Director, Industry Statistics and Economic Policy
To meet increased demand during the current global chip shortage, the semiconductor industry is substantially increasing its fab capacity utilization, a term that refers to the percentage of total available manufacturing capacity that is being used at any given time. Increasing semiconductor capacity utilization takes time, however. It is not as easy as “flipping a switch” and increasing chip output overnight.
[Learn more: Semiconductor Shortage Highlights Need to Strengthen U.S. Chip Manufacturing, Research]
When market demand runs high, such as in a cyclical market upturn like the one the market is in now, front-end semiconductor fabrication facilities, or fabs, will typically run above 80 percent capacity utilization, with some individual fabs running as high as between 90-100 percent. As the table below shows, the industry has been steadily increasing overall fab utilization over the past two years and is estimated to increase utilization even more during most of 2021 to meet demand. Higher fab utilization will increase chip output and allow the industry to fully meet the increased demand in the market.
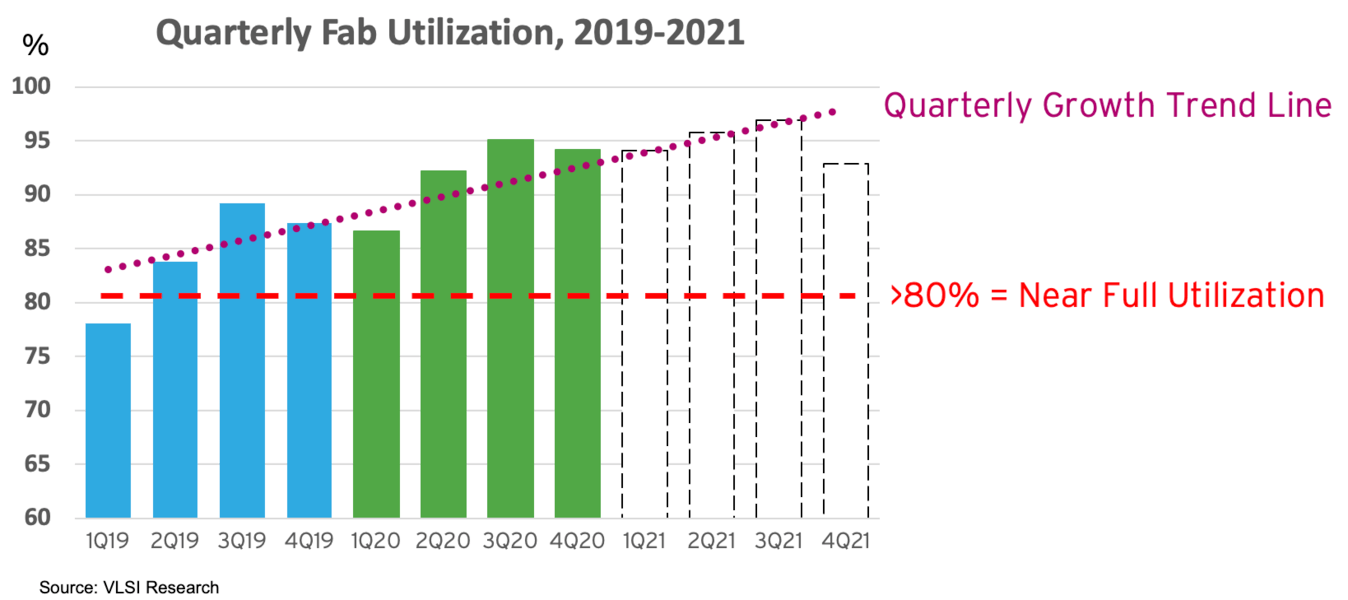
Unfortunately, increasing semiconductor capacity utilization takes time, because semiconductors are incredibly complex to produce. Making a chip is one of the most, if not the most, capital- and R&D-intensive manufacturing process on earth. The fabrication is intricate and requires highly specialized inputs and equipment to achieve the needed precision at miniature scale. There can be up to 1,400 process steps (depending on the complexity of the process) in the overall manufacturing of just the semiconductor wafers alone. And each process step typically involves the use of a variety of highly sophisticated tools and machines. In short, making semiconductors is exceedingly hard and, therefore, takes time.
How much time? Manufacturing a finished chip for a customer can take up to 26 weeks. Here’s why: manufacturing a finished semiconductor wafer, known as the cycle time, takes about 12 weeks on average but can take up to 14-20 weeks for advanced processes. To perfect the fabrication process of a chip to ramp-up production yields and volumes takes even much more time – around 24 weeks.
Then, once the fabrication process is complete, the semiconductors on the silicon wafer need to go through yet another stage of production known as back-end assembly, test, and package (ATP), before the chips are final and ready for delivery to the end customer. ATP can take an additional 6 weeks to complete. Therefore, the lead time, which is from when a customer places an order to receiving the final product, can take up to a total of 26 weeks. The table below provides some average times required in the chip fabrication process.
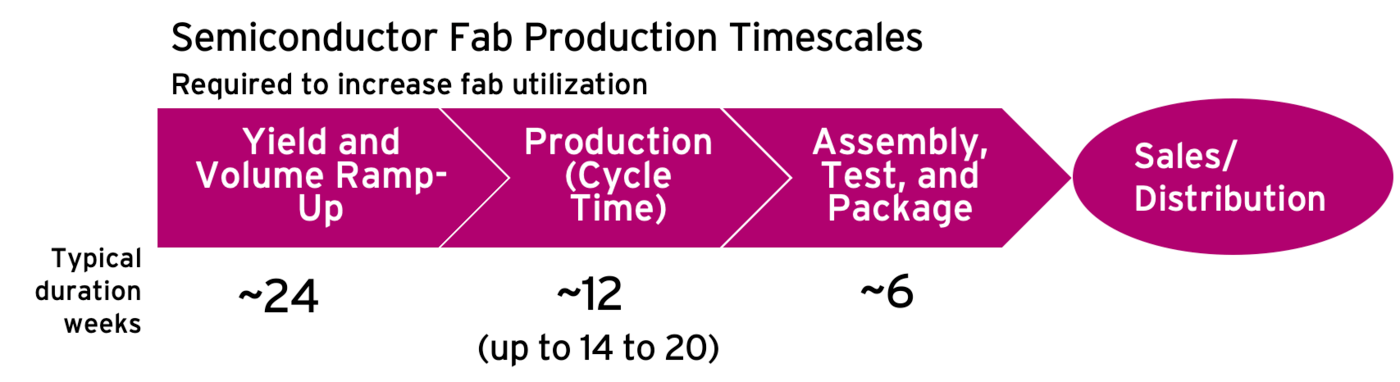
What this ultimately means is the semiconductor industry is currently doing all it possibly can in the short-term to increase utilization and meet increased demand both in the auto sector and more broadly for all customers. Forcing the industry to pick winners and losers by mandating who gets chips and who doesn’t will not overcome the time constant described above to fabricate a semiconductor.
The semiconductor industry has a wealth of experience operating in a complex supply chain to tap into for successfully navigating the challenges of the current demand environment. For example, besides increasing utilization and ramping up yields and volume, semiconductor firms are also creating command centers to assist with the most urgent customer requests and working closely with customers to ensure no doubling-ordering. These strategies are helping provide the quickest and most efficient delivery of product to customers during this challenging period.
Over the long-run, total global fab capacity will eventually need to increase to meet long-term demand growth for chips that cannot be met though increased utilization alone. The global semiconductor industry is planning accordingly to meet this projected market growth in the years ahead, through record levels of investment in manufacturing and R&D.
To help ensure the United States is home to a greater share of future chip innovation and production, SIA and a coalition of other business leaders, including those in the auto and medical device sectors, are urging President Biden and Congress to invest boldly in domestic semiconductor manufacturing incentives and research initiatives. Doing so will make more resilient America’s economy, national security, global technology leadership, and semiconductor supply chains.